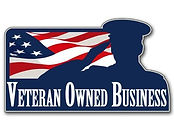

Igniting performance and empowering reliability!™
6 Steps to Maintenance Success!
C4 will join your team in performing criticality assessments for your facility. Our criticality assessments provide a structured approach to evaluate the importance of your equipment, processes, or systems, helping your team prioritize resources and maintenance efforts based on risk and impact. Paired with this, our scorecard review offers a clear, data-driven snapshot of performance metrics, highlighting strengths and areas for improvement in an easy-to-understand format. Together, these tools enable your team to make informed decisions, optimize operations, and align strategies with organizational goals during collaborative review sessions.
Our basic troubleshooting training equips teams with practical skills to identify, analyze, and resolve common operational issues efficiently, minimizing downtime and improving productivity. Complementing this, our Root Cause Analysis (RCA) training dives deeper, teaching participants how to systematically uncover the underlying causes of problems. Together, these programs empower employees to address immediate challenges and prevent recurring issues, fostering a proactive problem-solving culture within your organization.
Step1: Basic Troubleshooting/RCA Training
Step 2: Criticality Assessment and Scorecard Review
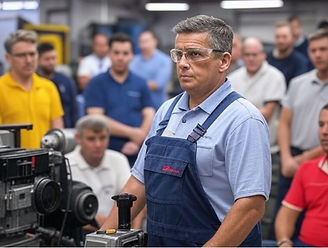

Step 3: Storeroom MRO overhaul/restructure
Step 4: Establish/overhaul the preventive maintenance program

Remodeling an industrial storeroom begins with aligning the layout and inventory with equipment criticality rankings, ensuring that high-priority parts for critical assets are easily accessible and adequately stocked. By integrating data into your ERP system from criticality assessments, we reorganize shelving, labeling, and storage systems to reflect usage patterns and minimize retrieval time for essential components. This tailored approach enhances operational efficiency, reduces downtime, and supports maintenance teams in keeping pace with the facility’s most vital equipment needs.

Establishing or overhauling a preventive maintenance (PM) program starts with assessing current equipment conditions and criticality rankings to develop a tailored schedule that targets key assets and minimizes unexpected failures. We then implement standardized procedures, incorporating best practices like routine inspections, lubrication, and part replacements, to extend equipment life and optimize performance. Finally, we integrate performance tracking and feedback loops to refine the program over time, ensuring it adapts to evolving operational needs and delivers measurable improvements in reliability.
Step 5: Implement Center-lining, inspection and lubrication programs within Operations
Step 6: Quarterly Auditing Program
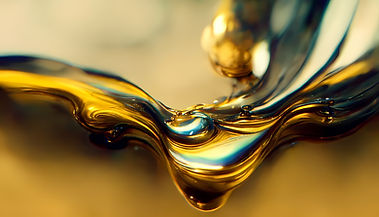
Establishing centerlines in your manufacturing facility involves setting baseline operational standards—such as temperature, pressure, or alignment settings—for equipment to ensure consistent performance and early detection of deviations. Inspection activities are then designed as routine, targeted checks to monitor these centerlines, identifying wear, misalignments, or other issues before they escalate into costly failures. Complementing this, lubrication activities are scheduled and executed with precision, using the right type and amount of lubricant to reduce friction and extend the lifespan of critical machinery components.
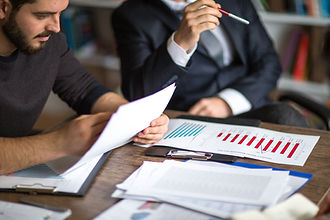
Establishing a quarterly auditing program begins with creating a comprehensive checklist that evaluates safety compliance, training effectiveness, SAP criticality data accuracy, parts management efficiency, and preventive maintenance program adherence. Each quarter, our team conducts thorough reviews, collecting data through inspections, employee interviews, and system analysis to identify gaps and ensure alignment with operational goals and regulatory standards. The findings are compiled into actionable reports, enabling continuous improvement across these critical areas and fostering a culture of accountability and reliability in your facility.